Pretty much moving my old thread here, with a better title that isn't limited to just one robot.
Having completed our first feather and competing at GSL/RoboChallenge champs, me and Dave feel like we've learnt so much that a new build is required!
We are hoping to make it to Germany in September, which gives us much longer than 3 weeks to build the robot unlike last time...
We were thinking something long the lines of biteforce/lockjaw grab/lifter. Here is a first pass design throwing some ideas around:
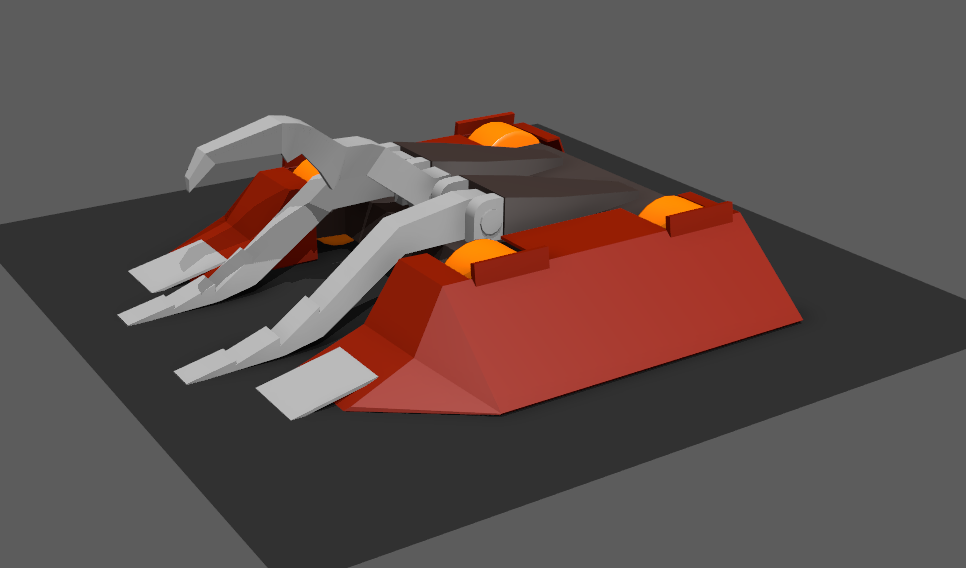
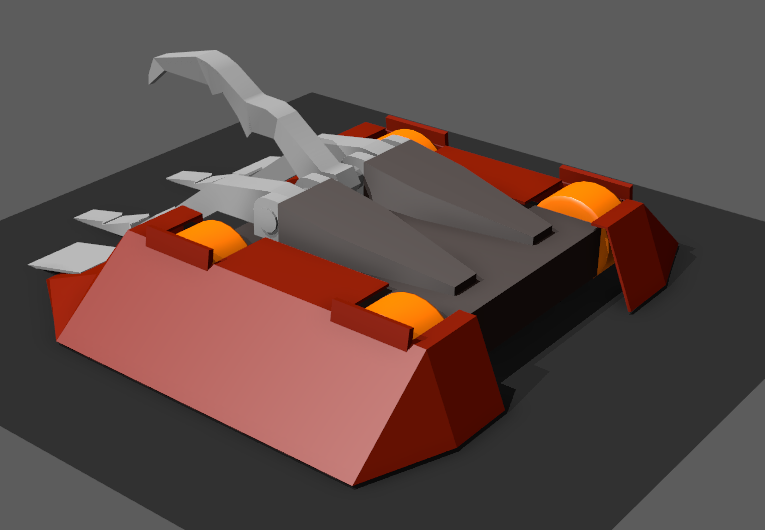
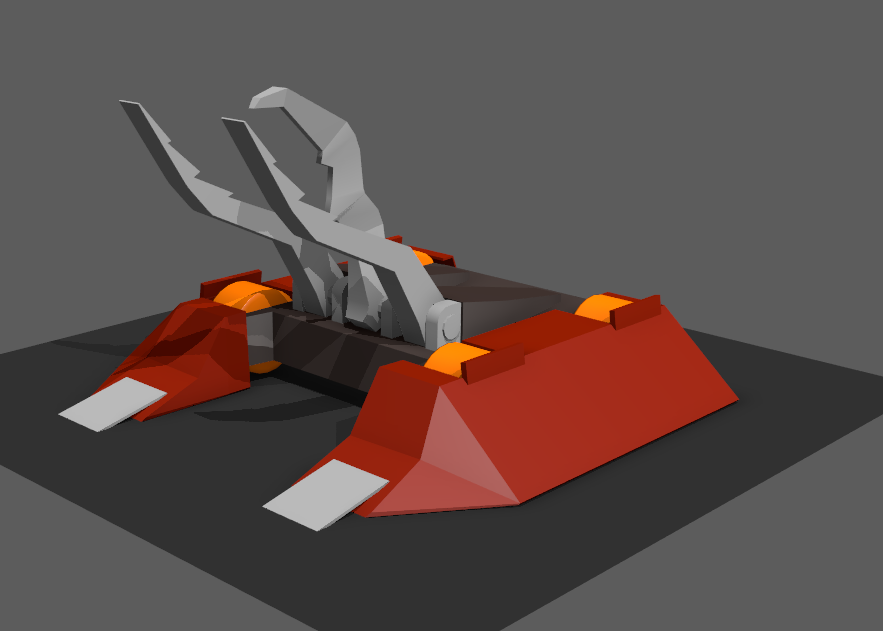
Will no doubt change tons before I start actually doing proper CAD files for it.
Having completed our first feather and competing at GSL/RoboChallenge champs, me and Dave feel like we've learnt so much that a new build is required!
We are hoping to make it to Germany in September, which gives us much longer than 3 weeks to build the robot unlike last time...
We were thinking something long the lines of biteforce/lockjaw grab/lifter. Here is a first pass design throwing some ideas around:
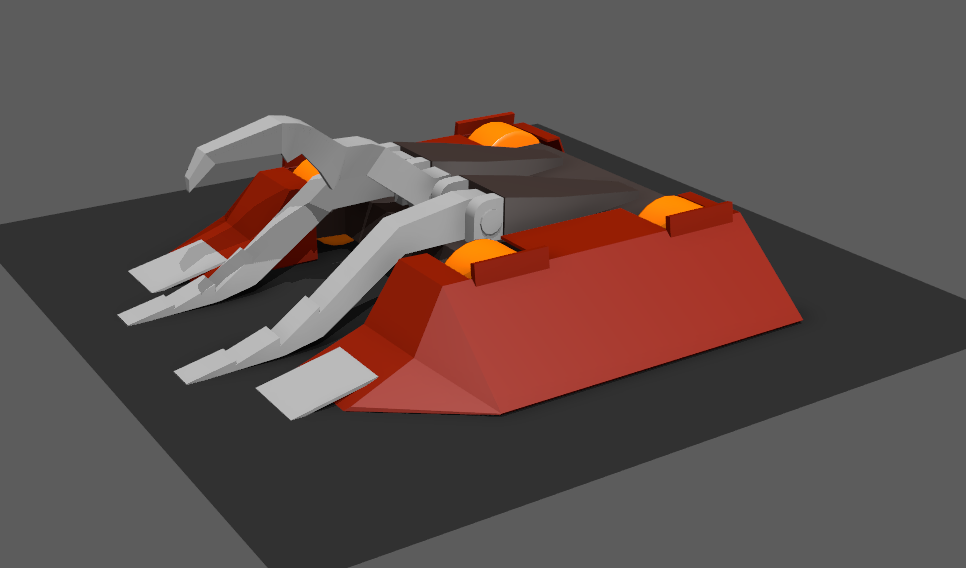
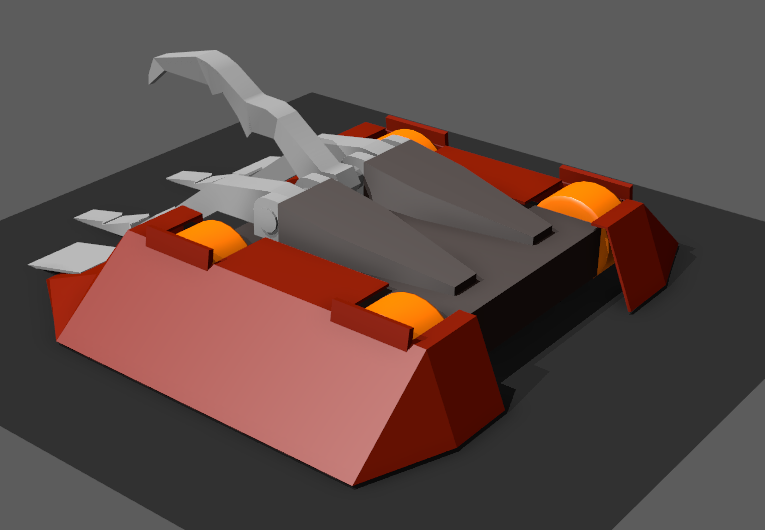
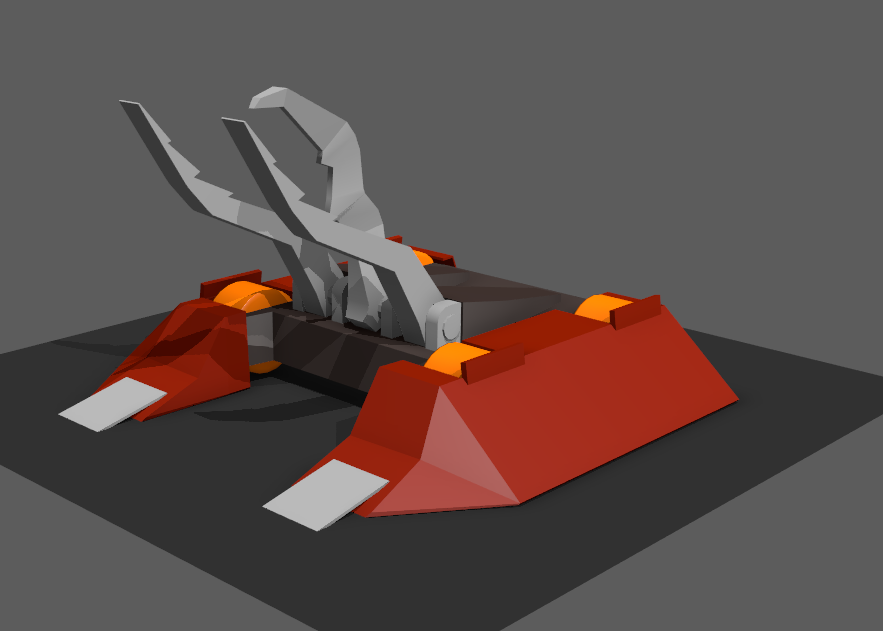
Will no doubt change tons before I start actually doing proper CAD files for it.
Comment